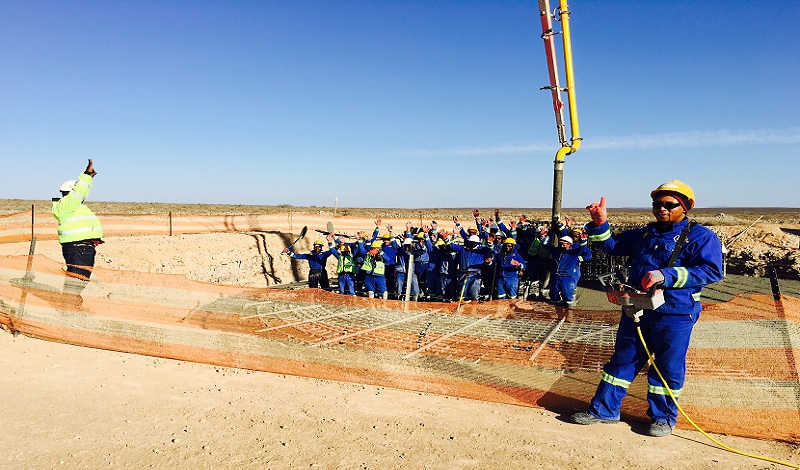
Khobab Wind Farm in the Hantam Municipality, Northern Cape, completed its first foundation pour on 30 June 2016. The foundations are designed using an 89% replacement of cement, one of the world’s lowest carbon wind farm foundation footprints, using the successful formulation its sister farm, Loeriesfontein Wind Farm, used in its foundations. All 61 foundations are due for completion by mid December 2016.
“We are currently testing an even higher cement replacement formulation and hope to achieve the desired strength test results soon,” explained Kevin Foster, project manager for Khobab Wind Farm.
The bases use a unique design comprising 35kgs of high grade Portland cement per cubic metre, almost 90% less than a standard concrete mix. This composition means that the wind farm’s carbon footprint is reduced to approximately 90.7kg of carbon dioxide per cubic meter. Ground Granulated Corex Slag (GGCS), a by-product from the iron industry, is used to replace 89% of the cement.
A twenty-eight day compressive strength test indicated that the 89% replacement ratio achieved an impressive strength of 55 MPa, and an expected ultimate strength of 100 MPa, within a fifty-six day period.
“The achieved reduction in our carbon footprint is phenomenal, especially considering that a standard 30-MPa concrete as supplied by the readymix industry equates to a carbon footprint of approximately 300 to 350 kgs of CO2 per cubic metre,” added Foster.
Traditionally, 30 MPa concrete requires between 300 kg and 350 kg of cement per cubic metre. But scientists working for Murray & Roberts have developed a technology that meets the 30-MPa standard using just 25 kg of cement or even less. Not only does it meet the standard, it far exceeds it. To date strengths of up to 52 MPa have been achieved on other sites using Murray & Roberts’ patented ARC (Advanced Recrystallisation) technology and 0 kg of portland cement per cubic metre.
More information from www.khobabwind.co.za